The Val Ease Central Railroad ©
Taking Z Scale to the Public Around the World
(Text and photos © Copyright Jeffrey MacHan)
Last Spike: A Märklin Factory Tour With Joe Rocchia
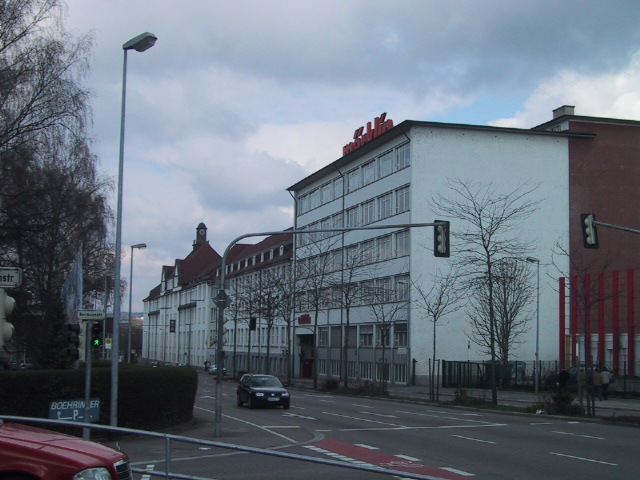
A visitor's first look at the Märklin factory in Göppingen.
Joe Rocchia or Herr Rocchia as he is known by his many colleagues and friends
at Märklin headquarters in the small Bavarian town of Göppingen has retired
after 26 years with the world's largest model train company. Normally one
would expect Joe to spend more time with his hobbies of Formula 1 racing,
cycling, photography and travel. (Yes, I did ask if he raced Formula 1 cars
and no, he doesn't!) Joe is not like most retirees. Although he is happy to
have retired from his responsibilities in the export department, he just can't
bring himself to turn in his Märklin employee badge. In fact he has decided to
stick around as guide for the English and Italian tours of the Märklin factory.

Jeffrey MacHan, Joe Rocchia, Terry Sutfin in the factory
courtyard.
And so it happened that Terry Sutfin, Eric Foxman and I were fortunate enough
to be the first official members of Joe's pre-retirement English test tour,
translated from the Italian. This was a wonderful sharing experience for the
guide and the guided. Joe was most anxious to jot down the proper English
terms for the tools, machinery, processes and materials that he
enthusiastically pointed out to us along the way. For our part, we were
anxious to wander off the beaten path and get close to fascinating and normally
restricted areas of the plant. Fortunately for Joe, my two colleagues were
largely well behaved although he sometimes had his hands full with yours truly
as I peeked and poked and asked an endless stream of questions.
Joe knew that his guests were primarily interested in the "Z" manufacturing
areas of the plant. His tour highlighted the various steps that went into the
production of our tiny trains. Early into the tour, Joe confessed to having
purchased a starter set in 1975. I suspect that our host had a starter set in
every scale Märklin produces, but I'll forgive him for humoring us.
Here in a nutshell, so to speak, are the high points of a Joe Rocchia Märklin
factory tour.
1. The two hour tour begins at 10 am in the courtyard where Joe points out that
the original factory was built in 1900. Several wings have been added to the
multistory building which houses 1200 of the 2000 Märklin employees. Other
plants operate in Hungary (tin-plating and gear production) and in Nuremberg
following Märklin's 1997 purchase of Trix.
2. Next we headed to the die-casting section where 20 employees operate several
125 tonne Frech presses. Here the mainly zinc alloys are melted at 400º
Celsius and injected into the Märklin-made molds every 15 seconds. The die-cast
parts are inspected, cleaned, milled, drilled, filed and polished before they
move on to the final sanding and touch-up area. The die-cast and injection
molds for the Trix 'Big Boy' were made by Märklin machinists at a cost of 2
million €. New design methods have reduced product development from 2 to 1.5
years.
3. The lathe department was incredible. Here long rolls and coils of various
metals passed through Chiron computer assisted manufacturing (CAM) drills and
milling machines to produce wheels and gears of all sizes. Believe it or not,
the largest machine-tool in the plant, a 5 meter long Tornos Moutier-Suisse
lathe, was churning out the smallest precision part, the "Z" scale side-rod
pins. The parts were so small that we needed a fine sieve to catch a pin from
the stream of cooling oil flowing into the collection bin.
4. Onward to the injection molding department where 35 workers made sure that
the 16 machines continued to pump out the hundreds of plastic parts and
components every 18 seconds. Five different types of plastics (ABS,
polystyrene, polyamide, polycarbonate, polyacetal) are used depending on the
durability, brittleness and color of the part. Unfortunately for us, most of
the machines were idle as Monday is set-up day. Then again, with only a couple
of presses in operation, we could hear Joe's explanations that molds for a
bumper cost 10,000 €, truck molds cost 24,000 € and a body shell mold is in the
neighborhood of 50,000 €. It was fun watching the part sorters vibrate and
shake a steady stream of parts until they fell into position for automatic
assembly.
5. Next we dodged the German language tour group to visit the galvanizing and
plating shop. In this area two very long plating machines provide the nickel,
chrome or gold finish to a myriad of parts. Here I learned that many track
components are actually zinc alloy with a nickel plating for conductivity.
6. The metal stamping shop was filled with older mainly manual presses where
employees fed the stock metal blanks into guides and activated the presses
which punched out the parts. During our visit most of the production were
wipers, contacts and gear blanks although we did see one bin of HO side rods.
Joe explained that the new automated presses are in Märklin's Sonnenberg plant,
a new facility built under government incentives to invest in the former East
Germany.
7. The painting shop was quite a surprise to me. Here the ubiquitous red stripe
on steam locomotive drive rods where painted by hand using a pressure-fed
stylus. The pad printing presses were busy adding road numbers to "Z"
reefers. One thing bothered me, however. The mainly women employees wielding
the airbrushes were not wearing respirators. Joe pointed out that the paints
were all water-based and they all worked under a painting hood. Undoubtedly
true, but if you suffer from asthma or a respiratory ailment, my advice to you
is to avoid the paint shop!
8. The last stop on Joe's tour was the final assembly and testing area. Here
we were in luck as the workers were actually putting together the blue 0-6-0
for the Fun starter set. Of equal interest to us was the incredible dexterity
demonstrated by the female workers who were hand riveting HO pantographs and
soldering the wiring harness onto printed circuit boards which would be
inserted further down the assembly line into the locomotive mechanisms.
The testing area was comprised of three workers who had the following tasks.
The first placed the locomotive onto an electrified cradle where they would be
run-in for 10 minutes. During our visit, 2-8-2 mechanisms were being tested.
Of the 10 on the test bed, at least 3 had binding and wobbles to be fixed.
The second worker had what appeared to be the torture test assignment. She
would take each graduate of the 10 minute test and place it on an oval of track
where it would be run around at full speed, stopped and started and then run in
reverse for about 15 seconds. One poor loco was under-performing and was
quickly taken in hand. The brushes were removed and repositioned and the
engine went through a second full-speed test run. Joe couldn't explain to me
why the QA did not include slow speed running of the locos. Just something for
the suggestion box!
The third worker had the task of packing the little gems into their shipping
boxes and then into the bins destined for the warehouse located at Märklin's
corporate headquarters and museum a few kilometers away. We had already
spotted the white Märklin delivery truck which shuttled between the two sites
all day long.
Alas, our time was up. We had managed to stretch our visit out to 12:30 but I
suspect that Joe will have his timing all worked out by the time you read this
account. Being ever curious, I managed to get some production info from Joe
before we parted company. We learned that "Z" scale represented from 10 to 15%
of production, of course "HO" had the lion's share at 80% and that Märklin's
Maxi (Gauge 1) line was actually the smallest proportion of production at 10%.
Reading about a Joe Rocchia Märklin factory tour simply does not compare with
the real thing. It is a must for every "Z" enthusiast who just happens to be
in the neighborhood of Göppingen. However, be forewarned, reservations are
required so don't expect to be able to just drop in at 10am and tag along.
Märkin is a German company, after all!
Oh, one last thing... Happy retirement, Joe. Ciao.
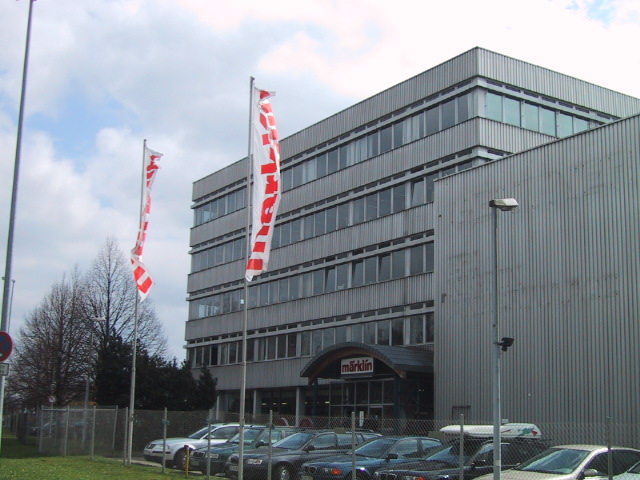
Märklin headquarters and museum.
|